Case Study
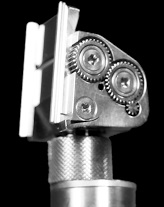
When Precision Is of the Utmost Importance, Owens Delivers
Lasik Surgery Device Machined to Perfection – Literally
Owens has a long history of machining ultra-precision, high tolerance parts for the medical industry. So when a Laser Surgical Instrument Development Company needed small precision parts made for a Laser Keratome, it came as no surprise they chose Owens Industries as their Machine Shop. When it comes to critical components used to alter or save human lives, we understand the importance of precision and accuracy – the results of our work demonstrate this understanding and dedication.
Once the client saw the work we had done on a few smaller precision parts for their Lasik Surgery Device, they asked us to manufacture the entire assembly (excluding the motor). This device (pictured to the right) features a high speed oscillating keratome (blade). The suction ring is attached to the cornea, and pressure is applied. The keratome assembly then moves with incredible precision and accuracy across the cornea to cut a flap which is about 160 microns thick. Since this is physically cutting the eye of a person (dictating whether their sight improves or worsens), every facet and feature of the assembly requires micron level tolerances.
A Lifetime of CNC Engineering Experience Improves Design of Critical Medical Component
When these parts were first created and tested, the customer’s initial design flaws became evident. The initial design would cause button-shaped holes instead of small flaps on the cornea. Though we do not offer design services, customers often ask us for help with capabilities studies for the manufacturability of their components. Lando, one of our manufacturing engineers who has been with us for 30 years, rose to the challenge when presented with these micron tolerances and 17-4ph stainless steel VAR (vacuum arc remelted stainless steel, which is a purer form). CNC machining is all Lando knows, and he knows it very well. Along with a couple others at Owens, he is considered to be among the top 1,000 CNC machinists in the country.
Lando was instrumental in assisting the customer to rethink their design, based on manufacturability – helping them achieve an even more precise assembly.
Wire EDM Cutting Used for Tight Tolerance Parts
The backlash of the gears was critical as the wire EDMed slots and mating rails. We had to achieve an 8 micro finish on the rails and the suction ring, ensuring the placement on the cornea was precise and smooth. The mating of the suction ring sliding inside the cutter required such precision and accuracy there was no room for tolerance variations. Using state of the art AGIE Wire EDM Machines, the cutter heads were wire cut using a .002” diameter wire. We were able to achieve a corner radii of .003”. The AGIE Sinker machines were used to create the pinion gears. Using this innovative technology, we manufactured the micro gears with almost zero backlash.
CNC Lathe / Turning Work Completed by Industry Leaders
The center bores of the gears for this Lasik Surgery Device required a tolerance within .0001” concentricity of each other. This work was tasked to our CNC Lathe / Turning Department – headed by Grub, an Owens’ employee since 1985. He joined Owens straight out of high school and CNC Lathe work is all he knows. He is the real old world machinist who can turn parts, the size of a pin head, on a manual lathe! The skill speaks for itself.
The bottom plate of the assembly required a micro finish, which we achieved with 5 axis CNC Milling. A precision micro boring head was used to make the posts, which had to match the .0001” concentricity of the gear centers. 5 axis precision CNC machining, along with Wire EDM, is what we do best!
With the exception of the motor and the optical/laser eye keratome blades (which were manufactured by Beckton Dickinson), Owens Industries manufactured every other component of this device, including:
- Miscellaneous Slip Fit Bushings
- PEEK Blade Holders
- Motor Housing
- The Knurled Coupler
- The Motor Plate
- Cutter Head
- Spline Gears
- Spring Loaded Pins
- The Suction Ring
- The Tube
The suction ring tube required deep hole drilling, and the insides had to be refinished with our Wire EDM. Due to the sensitive nature of this medical product, the recast layer of the Wire EDM needed to be cleaned out frequently. Owens has extensive experience deburring and creating surface finishes of critical medical components. Our old world skilled craftsmen are more than capable of hand-polishing such highly critical medical components, without affecting tolerances.
For medical components machined with the absolute highest precision, contact our CNC machinists at Owens today!
Get high-quality manufactured CNC components made with the best materials from Owens Industries.