EDM Machining
Owens Produces Intricate Shapes with Electrical Discharge Machining
Owens Industries is a leader in the EDM industry for producing complex parts with tight tolerances. With Owens, you get access to unique EDM and machining capabilities for OEM parts other competitors fail to match.
The Owens team can produce fine detail and surface finishes, precision gears, and complex cavities and shapes to meet your needs. Our dedication to quality and customer satisfaction sets us apart from any other competitor. When you hire Owens, you receive reliable components machined with high precision. Why settle for anything less?
Call upon the expertise of Owens Industries for problem parts or impossible components.
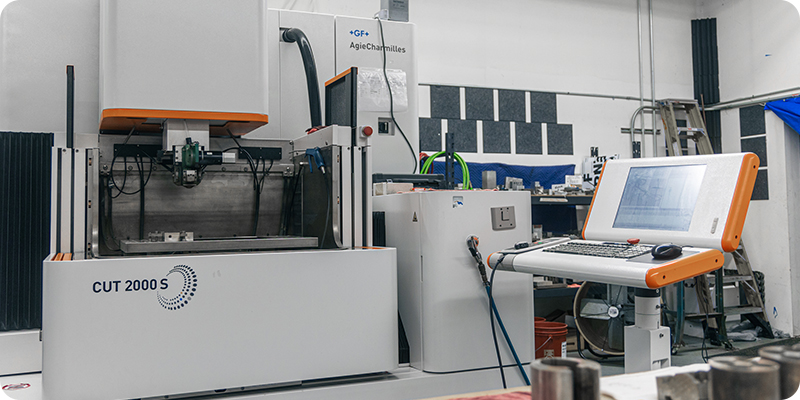
What are EDM Services?
EDM (electrical discharge machining) services refer to the application of non-conventional machining techniques that utilize electrical discharges or sparks to shape and mold hard-to-machine materials. These services are particularly valuable for creating intricate and precise components with complex geometries, often in industries such as manufacturing, toolmaking, and engineering.
Why Choose
Owens Industries for
EDM Manufacturing?
EDM achieves high machining tolerances. At Owens Industries, our state-of-the-art wire EDM machines ensure exact cutting for each workpiece. Unlike other CNC services, the EDM process maintains superior consistency by cycling new wire between spools, allowing repeatable wire cuts. Simultaneous cutting capability enables the wire to cut through stacked materials, increasing productivity. EDM's material compatibility extends to a wide range, from hardened metals like tungsten carbide to softer materials like copper. The process eliminates the need for additional finishing, as wire EDM cuts produce ultra-fine finishes, making products ready for use.
At Owens, we boast top-of-the-line equipment sourced from Switzerland. we have fine wire capabilities down to .002 inch diameter wire and we can offer 5 axis wire EDM capabilities with a fully integrated submersible ultra precision indexer.
Our EDM shop is committed to creating parts of the highest quality for your machining needs. Contact us today to learn how we can assist your project.
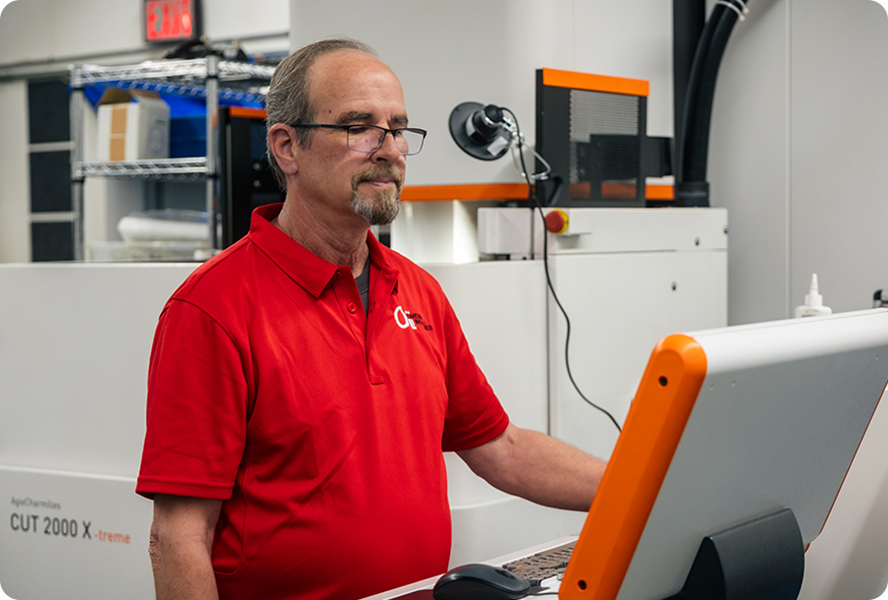
Types of EDM Services
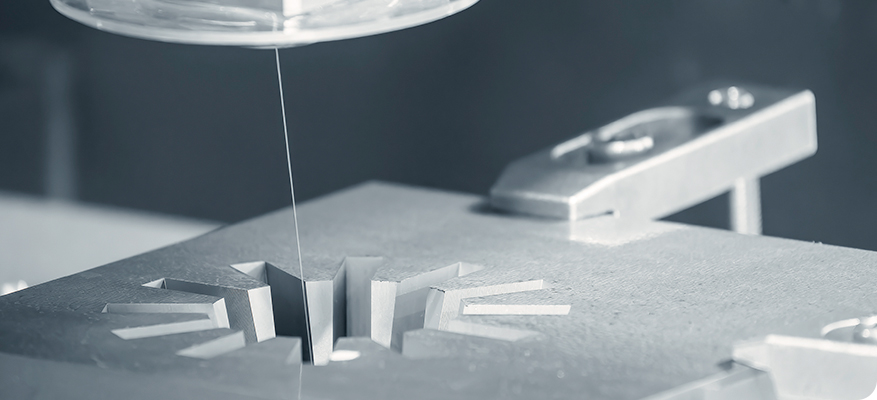
Wire EDM
Wire electrical discharge machining (Wire EDM) also known as wire-cut EDM or wire cutting, is a specialized machining process that uses deionized water as a dielectric, known for its precision and minimal burrs. Wire EDM employs a thin electrode wire, typically 0.1 to 0.3 mm in diameter, to cut without physical contact with the workpiece.
The more complex the product demands, the more ideal it is for wire electrical discharge machining. Wire EDM is best suitable for intricate and delicate parts, achieving accuracy within 1 micron with virtually no burrs. Wire EDM machines typically handle workpieces up to 16 inches thick. See more on how wire EDM works.
Our EDM Company uses Wire EDM to gain an edge in the CNC machining industry, promising clients ultra-precision micro-cutting with measurable results.
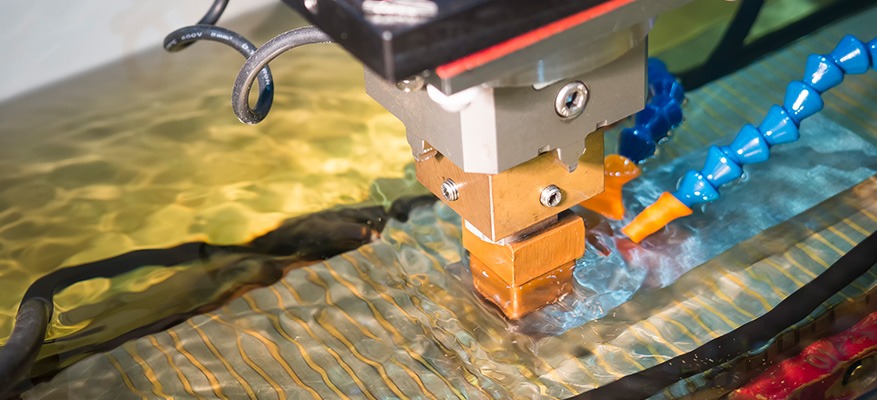
Ram/Sink/Plunge EDM
Sink EDM, also known as Ram EDM or Plunge EDM, is an EDM process used to produce precise, complex shapes in metal components. In this process, a specialized tool called an electrode is used to shape the workpiece by making repeated electrical discharges between the electrode and the workpiece.
Sink EDM is often used to produce shapes difficult or impossible to produce using other machining methods, such as high-precision holes, complex contours, and internal cavities. It is particularly useful for machining hard materials, such as tool steel and carbide, and can be used to produce parts with tight tolerances and smooth surface finishes.
View our Success Gallery to see our work!
Benefits of EDM Services
There are several benefits to using EDM in manufacturing:
- Precision EDM is capable of producing very precise shapes and cuts, with tolerances as low as 0.0001 inches. This makes it ideal for producing high-precision components, such as those used in the aerospace, medical, and electronics industries.
- No mechanical stress Because EDM uses electrical discharges rather than mechanical force to shape the workpiece, there is no mechanical stress applied to the material. This makes it ideal for machining delicate components or materials prone to distortion.
- Complex shapes EDM can be used to produce complex shapes difficult or impossible to create using other machining methods. It can create internal cavities, sharp corners, and contoured surfaces with ease.
- No tool wear In traditional machining processes, the cutting tool wears down over time and must be replaced. In EDM, the electrode does not come into contact with the workpiece and does not experience wear, so it can be used for virtually unlimited cycles.
- Hard materials EDM is very effective at machining hard materials, such as tool steel and carbide.
- High production rates EDM manufacturing can be used to produce a large number of identical components in a short period, making it suitable for high-volume production.
EDM Component Capabilities with Owens Industries
Common Components Created Through EDM Manufacturing With Equipment Made in Switzerland
Part | Application | Industry | Material | Specific Feature |
---|---|---|---|---|
Spray Nozzle | Urethane Application | Automotive | AISI 316 Stainless Steel | Locating Spray Slot within 0.0005" |
Inner Diaphragm | Hydraulic Flow | Energy Research | 6Al-4v Grade 5 Titanium | 4" Diameter Cylinder with 0.008" Thick Wall |
Actuator, Arm | Night Vision Goggles | Military | 17-4PH Stainless Steel Cond A | 20 Tooth Ratchet Profile |
Torsion Spring Pin Retainer | Retention Cap | Oil & Gas | 13CR-L80 NACE MR0175 | EDM Wire Curved Profile |
Hex Stop | Shaft Control Component | Oil & Gas | 4330 V MOD Steel | Matched Sets of Hexagon Rings |
Aperture Plate | Laser Alignment | Energy | Tungsten Nickel Alloy | 250 Micron Thru Holes |
Flexure | Electronic Control | Research and Development | AISI 303 Stainless Steel | EDM Wire 0.015" Wide Slot |
Spreader Tweaker | Pick and Place Device | Circuit Board Manufacturing | M2 Tool Steel | Fine Wire EDM Cut |
Plenum Base | Fuel Flow | Military | 6LA-4v Titanium per AMS 4928 | Machine 0.010" Thick Tube Wall |
Bottom Clamp | Microwave Reader | Research and Development | Glidcop AL-15 | 000-120 Threaded Holes |
Materials
EDM Machining Materials Trusted by Owens Industries
Our capabilities cover a wide range of materials to meet diverse client needs. Owens Industries has extensive experience manufacturing parts from different materials using Wire EDM:
- Brass
- Copper
- Stainless Steel
- Tool Steel
- Alloy Steel
- Aluminum
- Hastelloy
- Inconel
- Invar
- Maraging Steel
- Titanium
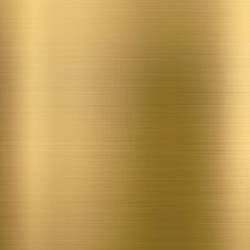
Brass
Brass is a metal known for its easy machinability and good electrical conductivity. It is ideal for applications requiring low friction, such as gears, locks, and musical instruments.
Brass | UNS Designation | DIN Designation | Alternative Designation |
---|---|---|---|
C36000 | UNS C36000 | CUZN39PB3 | CuZn39Pb3 |
C46400 | UNS C46400 | CuZn38Al | Naval Brass |
C93200 | UNS C93200 | Saems 660 | Bearing Bronze |
C48500 | UNS C48500 | CuZn39Sn1 | Leaded Muntz Metal |
C26000 | UNS C26000 | CUZN30 | Cartridge Brass |
C37700 | UNS C37700 | CUZN40PB2 | Forging Brass |
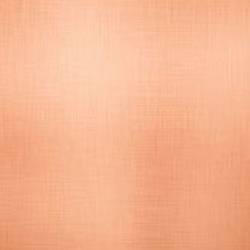
Copper
Copper is excellent at conducting heat and electricity, making it perfect for electrical uses like busbars and wire connectors. It is easily recognized by its shiny reddish-orange color and is also used in plumbing and roofing.
Copper | UNS Designation | DIN Designation | Alternative Designation |
---|---|---|---|
C11000 | UNS C11000 | Cu-ETP | Electrolytic Tough Pitch (ETP) Copper |
C10100 | UNS C10100 | OF-OK | Oxygen-Free Electronic (OFE) Copper |
C10200 | UNS C10200 | OF-Cu | Oxygen-Free (OF) Copper |
C28000 | UNS C28000 | CuZn40 | Muntz Metal |
C14500 | UNS C14500 | TeCu | Tellurium Copper |
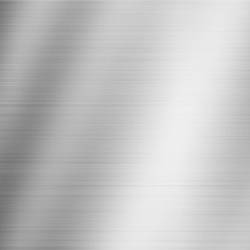
Stainless Steel
Stainless steel is known for its strength, heat, and corrosion resistance, along with its durability and attractive appearance. These qualities make it suitable for a wide range of uses, including kitchenware, medical instruments, and construction.
Stainless Steel | UNS Designation | DIN Designation | Alternative Designation |
---|---|---|---|
316L | UNS S31603 | X2CrNiMo17-12-2 | Stainless Steel 316L |
304 | UNS S30400 | X5CrNi18-10 | Stainless Steel 304 |
17-4 PH | UNS S17400 | X5CrNiCuNb16-4 | Stainless Steel 17-4 PH |
303 | UNS S30300 | X8CrNiS18-9 | Stainless Steel 303 |
420 | UNS S42000 | X20Cr13 | Stainless Steel 420 |
440C | UNS S44004 | X105CrMo17 | Stainless Steel 440C |
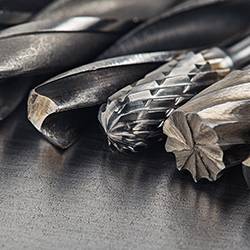
Tool Steel
Tool steels are hard, stiff, and resistant to abrasion, making them perfect for manufacturing industrial tools. Their robustness is essential for cutting, drilling, and molding applications in various industries.
Tool Steel | UNS Designation | DIN Designation | Alternative Designation |
---|---|---|---|
D2 | UNS T30402 | 1.2379 | X155CrVMo12-1 |
M2 | UNS T11302 | 1.3343 | HS6-5-2C |
A2 | UNS T30102 | 1.2363 | X100CrMoV5-1 |
S7 | UNS T41907 | 1.2355 | 50CrMoV13-15 |
O1 | UNS T31501 | 1.2510 | 100MnCrW4 |
H13 | UNS T20813 | 1.2344 | X40Cr |
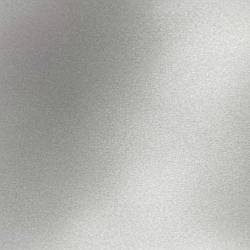
Alloy Steel
Alloy steels include additional elements beyond carbon, which improve their hardness, toughness, and resistance to fatigue and wear. These steels are widely used in construction, automotive, and machinery due to their enhanced properties.
Alloy Steel | UNS Designation | DIN Designation | ISO Designation |
---|---|---|---|
4140 | 1.7225 | 708M40 | 42CrMo4 |
4340 | 1.6565 | 817M40 | 40NiCrMo6 |
8620 | 1.6523 | 805M20 | 20NiCrMo2 |
52100 | 1.3505 | 100Cr6 | SUJ2 |
4142 | 1.7227 | 708M40T | 41CrMoS4 |
6150 | 1.8159 | 735A51 | 50CrV4 |
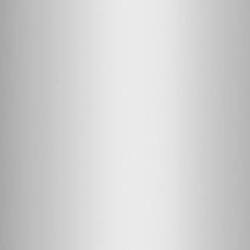
Aluminum
Aluminum alloys are lightweight and strong, with excellent thermal and electrical conductivity. They are also resistant to corrosion and can be anodized for added protection, making them ideal for aerospace and packaging industries.
Aluminum Alloy | UNS Designation | DIN Designation | ISO Designation |
---|---|---|---|
7075-T651 | 3.4365 | 76528 | AlZn5.5MgCu |
6082-T651 | 3.2315 | 64430 | AlSi1MgMn |
6060 | 3.3206 | EN AW-6060 | AlMgSi |
5052 | EN AW-5052 | 3.3523 | AlMg2,5 |
2017A | 3.1325 | 24530 | AlCu4MgSi |
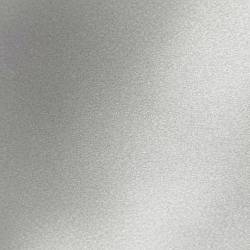
Hastelloy
Hastelloy is a group of nickel alloys known for their high resistance to corrosion, pitting, and stress-corrosion cracking. They are often used in harsh environments like chemical processing and aerospace, where durability is crucial.
Hastelloy | UNS Designation | DIN Designation | Alternative Designation |
---|---|---|---|
C276 | UNS N10276 | 2.4819 | NiMo16Cr15W |
C22 | UNS N06022 | 2.4602 | NiCr21Mo14W |
B-2 | UNS N10665 | 2.4617 | NiMo28 |
X | UNS N06002 | 2.4665 | NiCr22Fe18Mo |
C2000 | UNS N06200 | 2.4675 | NiCr23Mo16Cu |
G-30 | UNS N06030 | 2.4603 | NiCr29Mo9Fe |
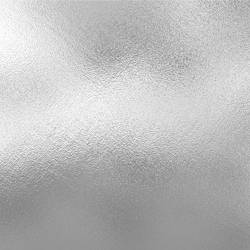
Inconel
Inconel is a strong, corrosion-resistant nickel alloy, ideal for challenging aerospace applications. It can withstand extreme temperatures and pressures, making it suitable for jet engines and gas turbines.
Inconel | UNS Designation | DIN Designation | Alternative Designation |
---|---|---|---|
718 | UNS N07718 | 2.4668 | NiCr19Fe19Nb5Mo3 |
625 | UNS N06625 | 2.4856 | NiCr22Mo9Nb |
600 | UNS N06600 | 2.4816 | NiCr15Fe |
X-750 | UNS N07750 | 2.4669 | NiCr15Fe7TiAl |
601 | UNS N06601 | 2.4851 | NiCr23Fe |
725 | UNS N07725 | 2.4668 | NiCr19Fe19Nb5Mo3 |
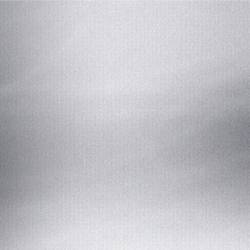
Invar
Invar is a nickel alloy with very low thermal expansion, making it highly stable and perfect for precision applications such as instrumentation and aerostructure molds. It is also used in scientific instruments where dimensional stability is critical.
Invar | UNS Designation | DIN Designation | Alternative Designation |
---|---|---|---|
36 | UNS K93600 | 1.3912 | FeNi36 |
42 | UNS K94200 | 1.3917 | FeNi42 |
48 | UNS K94800 | 1.3922 | FeNi48 |
32-5 | UNS K94610 | 1.3911 | FeNi32-5 |
42-6 | UNS K94620 | 1.3913 | FeNi42-6 |
46 | UNS K94630 | 1.3914 | FeNi46 |
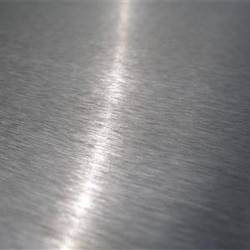
Maraging Steel
Maraging steels are ultra-high-strength steels that are easy to machine and weld without causing distortion. They gain their exceptional hardness and toughness from a special heat-treating process, making them suitable for aerospace and tooling applications.
Maraging Steel | UNS Designation | DIN Designation | Alternative Designation |
---|---|---|---|
200 | UNS K93120 | 1.6359 | 20Ni Maraging Steel C200 |
250 | UNS K92890 | 1.6358 | 18Ni Maraging Steel C250 |
300 | UNS K93120 | 1.6354 | 18Ni Maraging Steel C300 |
350 | UNS K93160 | 1.6356 | 18Ni Maraging Steel C350 |
400 | UNS K91460 | 1.6352 | Custom 465 Stainless |
500 | UNS K92810 | 1.6354 | Custom Age 625 Plus |
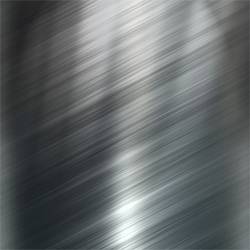
Titanium
Titanium is a lightweight metal with excellent strength, low thermal expansion, and high corrosion resistance. Its ability to be sterilized and its biocompatibility make it unique, especially in medical implants and aerospace components.
Titanium Grade | UNS Designation | DIN Designation | Alternative Designation |
---|---|---|---|
5 (Ti-6Al-4V) | UNS R56400 | 3.7165 | Ti-6Al-4V |
2 | UNS R50400 | 3.7035 | CP Titanium |
23 (Ti-6Al-4V ELI) | UNS R56401 | 3.7165 | Ti-6Al-4V ELI |
9 (Ti-3Al-2.5V) | UNS R56320 | 3.7195 | Ti-3Al-2.5V |
7 (Ti-0.2Pd) | UNS R52400 | 3.7235 | Ti-0.2Pd |
12 (Ti-0.3Mo-0.8Ni) | UNS R53400 | 3.7105 | Ti-0.3Mo-0.8Ni |
Tolerances
Owens Industries’ Achievable EDM Machining Tolerances
Our EDM (Electrical Discharge Machining) capabilities are designed for parts that require ultra-precise tolerances of up to ±0.00005 inches. This precision level is crucial for components with intricate features and complex shapes, especially in industries like defense, optics, and medical devices. EDM machining at Owens allows for a minimum feature size of 0.01" x 0.01" x 0.01" and a finish as smooth as Ra 8μin, making it the go-to process for small, detailed parts where precision is non-negotiable. With a 12-week standard lead time, our EDM machining ensures your critical parts are delivered accurately and on time.
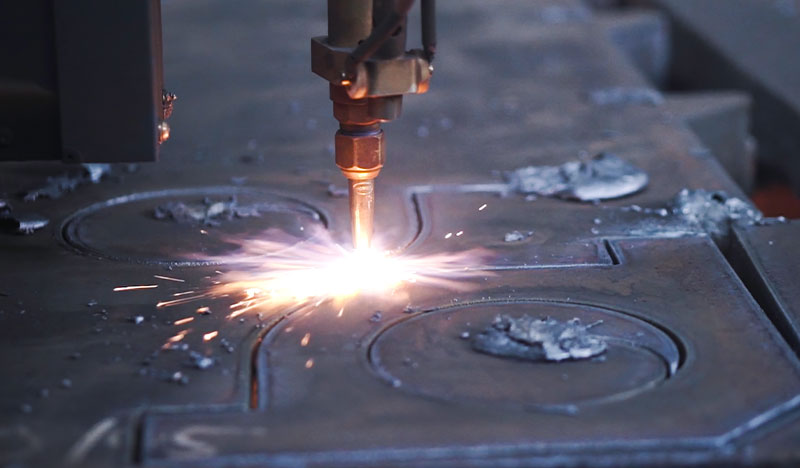
Attribute | Value |
---|---|
Maximum Part Size | 13.5" X 21.5" |
Standard Lead Time | 12 weeks |
General Tolerances | .0005" |
Precision Tolerances | .00005" |
Minimum Feature Size | .01 X .01 X .01 |
Minimum Surface Finish | 8 |
Standard Surface Finish | 64 |
*Standard delivery dependent on workloads. Call Owens for current lead times.
Industries
Providing 5-Axis Wire EDM Capabilities for Several Industries
Owens Industries offers true rotary axis indexing Wire EDM, true 5-axis wire EDM systems developed in partnership with European and Japanese manufacturers, sink EDM capabilities, and close tolerance 5-axis CNC machining.
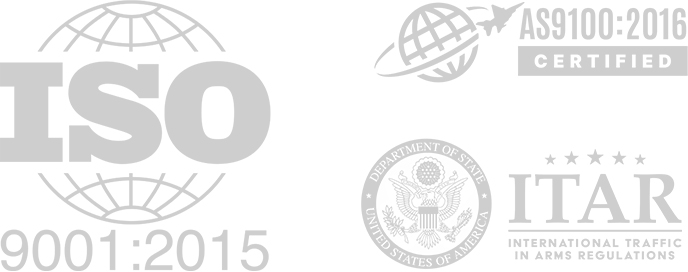
FAQ
EDM Machining Frequently Asked
Questions
What is Electrical Discharge Machining?
EDM, also known as spark machining, is the cutting process that erodes materials with an electric spark, created between an electrode and the machined part. The electric spark produces a flow of energy between the machine and the part, which will melt away the unwanted areas on the part.
What is Wire EDM?
Wire EDM is slightly different from traditional EDM, as the spark created in Wire EDM is always produced in deionized water. This is used in Wire EDM because it is not a fire hazard when the spark is created.
What is the difference between wire EDM and sinker EDM?
Sinker EDM uses a custom electrode to plunge into the material, while wire EDM cuts through the material with an electrode wire. While both methods utilize the same means of eliminating material, wire EDM cuts fully through the material. Sinker EDM is designed to only go part of the way through the piece.
How does Wire EDM work?
Wire EDM uses a metallic wire, typically made of brass or copper, to cut the part. Voltages have to be measured between the part and machine before cutting can occur. The process used is dependent on the accuracy and finish needed.
What is the surface finish of EDM?
EDM allows for a very fine almost mirror-like finish when multiple skimming passes are made.
What industries are Wire EDM used in?
Industries that produce precision-dependent components requiring fast manufacturing times use Wire EDM for repeatable accuracy. These industries include medical devices, aerospace, optical equipment and more.
What are the benefits of Wire EDM?
Some benefits of Wire EDM machining include superior consistency, simultaneous cutting, material compatibility and eliminating finishes. This machine type has one of the closest machining tolerances available today.